CCTV is an extremely beneficial piece of technology that is useful to anyone and everyone! Whether you are a business owner or a homeowner, CCTV installation is definitely something worth investing in.
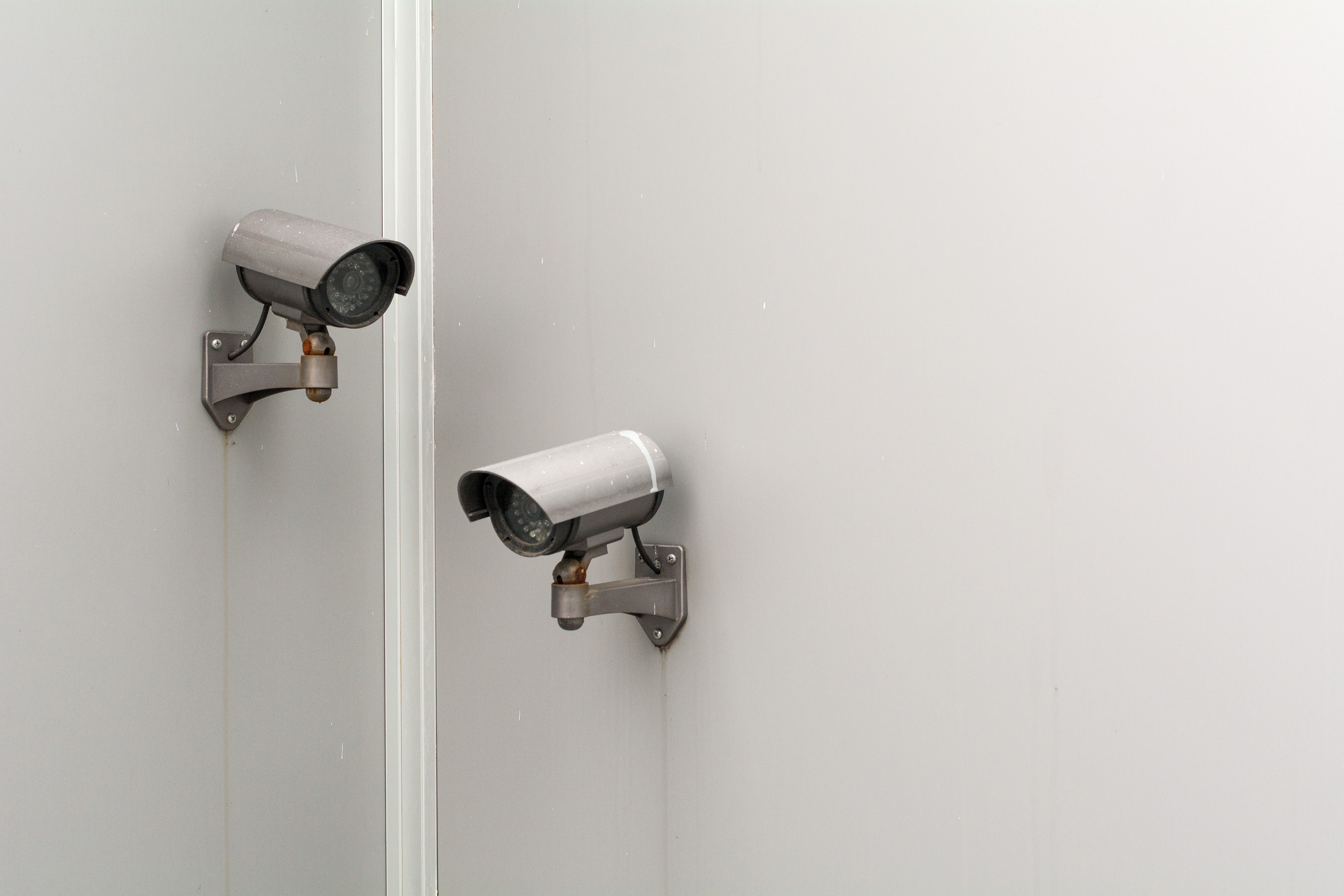
Benefits of CCTV installation
Arguably the most beneficial aspect of having CCTV is the peace of mind that it brings. Even if there’s never a reason for you to watch your CCTV footage back, at least you have it there just in case. CCTV installation has been at the top of many people’s to do list when buying a new building, especially a business building. Monitoring those who are coming in and out of the premises can be ideal for capturing all sorts of things.
In addition, CCTV installation is becoming more popular amongst homeowners as it’s a huge deterrent to potential crime opportunities. Whilst it deters people from your home, you could also be helpful to those around you should they not have CCTV installed on their property. CCTV installation will also reduce your home insurance costs as some insurance companies will offer discounts for those who have it installed. Similarly, to this, in some cases employees are often responsible for their own property theft, therefore having CCTV installation at your business can help provide a safer working environment as well as evidence if necessary.
Best type of CCTV cameras
One type of CCTV installation that is very useful is, pan tilt zoom cameras can be moved in a 360 direction and also can zoom in closer if needed to capture detail. They’re designed to cover large areas and therefore are ideal for places such as farms, shopping centres or car parks.
Fisheye cameras offer both 180 and 360 panoramic perspectives of the areas that they are monitoring. Generally, a small device so perfect for being more discreet compared to the obvious outstanding ones. These types of cameras are perfect for casinos or in retail when it’s useful to have detailed but discreet cameras that can pick up on hidden sneaky tricks that customers often try to pull.
Automatic number plate recognition (ANPR) is a device most utilised by police or road traffic cameras. It automatically recognises a vehicle’s registration which is handy for the cases of unidentifiable crime, illegal parking, and speeding.